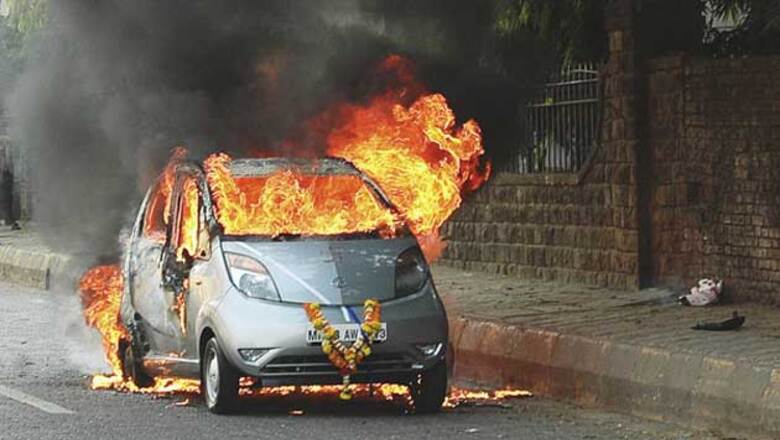
views
By all accounts, March 21 was an uneventful muggy Mumbai summer’s day. Steaming traffic jams were spread thickly over the city roads. Most people were sweating it out in BEST buses. Nutan Sawant was not one of them. That day she was in a car. For as long as she could remember, she had travelled on those lifelines of Mumbai: Local trains and buses. And then in October 2009, her husband Satish heard about the launch of the Rs 1-lakh people’s car. “Last year after Diwali, I thought we could afford a small car,” he says. He was so keen that he jumped the queue by paying Rs 15,000 to a Concorde Motors employee. March 21 was when they had to collect it. Satish and his wife went to the Concorde showroom at 10 a.m. Since Satish didn’t know driving, Concorde arranged for a driver. It was a great feeling for Nutan and Satish. They relaxed in the spacious rear seat as it glided through the tree-lined roads of Prabhadevi. They had travelled 15 km when Nutan sniffed, turned towards Satish and asked the Rs 2.26-lakh question: “Do you smell something burning?”
Satish was unsure. More so when the driver said a new car could have such a smell. They travelled a bit further and still the smell wouldn’t go away. Nutan again expressed her concern. When Satish or the driver did not pay any heed, she ordered the driver to stop the car. A biker passing by drew their attention towards the rear part of the car. The Sawants and the driver got out to look and saw smoke first and then fire. Satish or Nutan don’t quite remember the exact sequence of events except that in 15 minutes, the entire car was completely gutted. Sawant called Concorde. They towed the car away. The police, too, turned up but were unsure of what complaint to register. The Sawants returned home by 2.30 p.m.; without the car of course.
The dark edge of a dream
Take the image of a burning Nano and put it next to the image that actually gave birth to the idea of Nano. One version (now declared apocryphal) says Ratan Tata saw a family of four on a bike in pouring rain and decided to come up with a car that cost less and carried more.
The target sale price of the car was Rs 1 lakh, less than half of the price of cheapest car available in India and indeed anywhere in the world.
To make sure that the promise was kept, Tata Motors turned on the innovation tap. The engineers at Tata Motors questioned everything. The result was a fresh new design. The engine went to the rear and the petrol tank in the front. A lot of fibre and plastic was used instead of steel to keep the weight of the car low.
The nearly 100 vendors all understood the design to deliver the goods. The approach worked.
Ratan Tata announced the car in New Delhi Auto Show in January 2008, the news of the $ 2,500 car spread right across the world. The publicity buzz rivaled that of any of Apple’s products. The potential was huge. The Nano can add Rs. 1,000 crore, or about 3 percent of annual revenues to Tata Motors, says analyst Vaishali Jajoo of Angel Broking. It will also fit in with global ambitions of the company which has already planned to launch Nano in Europe in 2011.
All that this car could achieve hangs in balance because of the fire in Sawant’s car. Now this isn’t the first time that cars have caught fire in India. But so many cars of a model in such a short interval are worrisome. Just seventeen days after the Sawant incident, on April 7, another Nano caught fire on the National Highway 8 near Anand in Gujarat. These incidents are worrying the customers about the safety aspect of Nano. Tata Motors dealers who spoke to Forbes India said these customer concerns were straining the dealer-company relationship.
One way Tata Motors could soothe customer nerves is to recall all the vehicles sold till now, fix the problem and then re-release the product back in the market. Now that’s an ethical dilemma. In India, a full-blown recall would just hurt the brand very much.
Anyway, there are no regulators for this kind of thing in India. India needs a full-fledged organisation like the National Highway Traffic Safety Administration (NHTSA) in the US that examines the cause of accidents and establishes better safety norms, a senior manager at a global firm says. “We regulate many other things so well. Why not auto customer safety?”
Tata Motors, for now, is busy investigating. “We are conducting our investigations which will be completed soon,” says a Tata Motors spokesperson. Since the Nano is a marquee and highly sensitive project most people -- insiders, suppliers, ex-employees, competitors — who spoke to Forbes India did so on the condition of anonymity. Tata Motors itself chose to respond to our questions via an email.
The two recent fire incidents have come as a bolt to Tata Motors that had all along believed the fire problem had been sorted out last year itself.
First fires: in a smoke cloud
Actually, Tata Motors calls them “smoke”. But there is rarely smoke without fire. So let us call it the first round of fire incidents. There were in all five such incidents -- three were reported in the media and two weren’t -- and they all took place last year.
The first incident was reported from Ahmedabad. A Nano (GJ 1KA 4648) parked at Vaibhav Gokul Bungalows in Ahmedabad suddenly caught the attention of Jayanti Patel when he heard a loud noise outside his house at around 12:30 p.m. on Sunday, September 13, 2009. Patel noticed smoke coming out of neighbour Ravindra Bhagat’s Tata Nano. Bhagat was not at home. With the help of a few neighbours, Patel broke one of the window panes and doused the fire emanating from around the car’s steering wheel. Almost thirty minutes and after pouring fifteen buckets of water, they saved the Nano from any major damage.
Over the next month, two similar incidents were reported from New Delhi and Lucknow. It was a sticky situation for Tata Motors. All three owners, Bhagat, Sunil Kumar Panwanda from New Delhi and R.H. Rizvi from Lucknow, expressed concern and shock. “I drove the car for about two hours and then parked it at home. After an hour, my kid [came] running inside saying that the car is on fire. I rushed outside and saw the steering wheel burning,” says Panwanda.
Within no time, Tata Motors attended to these cars, repaired and returned them to the owners. It attributed the problem to a short circuit in the combination switch area. And then, the company said that it will carry out a pre-emptive check of all the 7,500 cars that it had sold by then. As it turned out, the problem was indeed with the combination switch, a steering column switch assembly that manages the car’s headlamps, indicators and wiper blades.
Tata Motors hasn’t specified the underlying problem that led to the short circuit. This is all that a company spokesman would say: “The three incidents of ‘fire’ that are being referred to were actually not fires but noticing of smoke and localised meltdown of plastic parts due to short-circuit in these cars’ combination switches. As announced earlier, the issue has been rectified.”
A Tata Motors official, speaking on the condition of anonymity, said Shutham Electric, a Pune-based company that was supplying the combination switches, was not able to deliver consistent quality. Shutham Electric has for long been a trusted supplier for Tata Motors. It has supplied switches for Indica, Safari, Indigo and the Vista models besides products of Mahindra & Mahindra, Nissan and Fiat.
Tata Motors inside sources say it was only in early 2009 that Shutham started struggling to meet the increased demand from its existing capacity. “Supplies from Shutham were delayed which was holding up production,” says a Tata Motors official who didn’t want to be quoted. Also Shutham was going through a rough patch in the aftermath of the global recession. When Forbes India contacted Samarjit Bose, Shutham’s managing director, he declined to comment.
In mid 2009, Tata Motors engaged Gurgaon-based Minda to replace Shutham. With Minda, the first leg of the problem seemed resolved. There have been no “smoky” fires being reported after that.
Second fire: Whodunnit?
But that certitude and peace now stand shattered with the the two fires. This time, there is no doubt whether it is smoke or fire. What could go so wrong that the entire car goes up in flames? Forbes India decided to do its own research.
Of the two cars that burned down this year, the one on NH8 was company-owned. We spoke to the owner of the other, Sawant. We also located two of three Nano owners of the last year’s “smoke-fire” incidents. We then got in touch with two Bangalore based car enthusiasts, Uday and Shramik Masturlal, who have bought a Nano each. We also contacted an automobile expert-cum-rally driver who modifies his own cars and who prefers to remain anonymous. This man is rated very highly for knowledge on www.teambhp.com , an online site that caters to automobile enthusiasts.
Our expert disassembled the Nano completely to understand the design and came with a few hypotheses about why some Nanos may be catching fire. We must say that since we don’t have access to either Nano designs or Tata Motors’ engineering insight, what we have are only possibilities.
Every deduction must have a starting axiom. Ours is that a fire that completely burns the car down has to do something with petrol. Without the fire coming in contact with petrol it would be hard for it grow to the extent that its burns the car down in minutes.
Our expert identified the prime suspect. It is a cheap part that goes by various names: Banjo bolt, clip or a coupler (see photo). Basically, this is a small cylindrical connector that joins the petrol pipe coming from the fuel tank to the fuel rail, which is a metal pipe that delivers petrol to fuel injectors in a car engine. Our expert feels that the banjo bolt is flimsy and could spring a leak if not attached properly.
The place where this bolt is located is too close to a sensor connector and the fire wall. Now, if the bolt springs a leak, the petrol would end up on the engine block which could lead to a fire at a high enough temperature.
We got this explanation checked by another automotive expert working a large automotive company. “It is also possible in many cases that the banjo bolt case that the actual assembly of the part was not done right, that is wiring too close to a ‘hot’ part, or an improper connection, or the clip may not have been installed correctly,” he says.
Tata Motors’ doesn’t think so. “People can have their views, rightly or wrongly, on many aspects of any product. Suffice it to say that we have taken all precautions and met with all the tests to ensure a safe car. In fact, the connector is not flimsy at all. It is actually sophisticated in so far as it gives the operator a feedback on when it is properly mounted. The fuel line material and routing is what you will find in many cars of this and higher segments -- again it is state-of-the-art or better,” said the Tata Motors spokesperson.
Where is the fault line?
Admittedly, it would be very difficult for Tata Motors to do forensics because both vehicles have been burnt completely. Yet, one must ask a question? Is this a design problem? After all, Nano’s design is a novel one. If the design is at fault then it has serious implications for the 30,000 Nanos that have already been sold.
At the moment though, it doesn’t appear to be a design problem, at least not in case of the incidence of smoke coming out of the steering wheel. “If it was a design failure, it would have been seen in many more cars. But, you can see that the initial steering wheel fire incidents were few. So, it is likely that a particular batch of combination switches was the problem,” says a senior automotive professional. As it turns out, some key component suppliers who are privy to some of Tata Motors plans say that almost 100 Nanos were each driven 100,000 kilometres after the combination switch fires and there no problem that was detected. It would then appear that even the recent two fires aren’t because of a design flaw.
The next most plausible explanation, which Tata must investigate, is that some suppliers cut corners. This gave rise to a bad batch of faulty vehicles and which somehow ended up in the market. This could have happened when the siege at Singur was on. Tata Motors was forced to shift production temporarily to Pantnagar in Uttarakhand.
“And then post Singur, everything was put in fourth gear,” says a supplier. Tata Motors wanted the Nano out as quickly as possible. “There was a lot of pressure from the top management to launch the Nano even though they had concerns about the noise, vibration and harshness of the engine. And the deadline was the Geneva Motor Show (March 2009),” says a Tata Motors official.
Tata Motors had had a spate of bad news: JLR acquisition issues, the commercial vehicle market slowdown and it perhaps wanted to give some good news. And suddenly everybody was under enormous time pressure. “A vendor knows his product very well but transferring that knowledge to Singur, Pantnagar or Sanand in the short time frame was a challenge,” adds the supplier. Some other suppliers talk about how they had to ramp up from 3,000 units a month to 15,000 units a month of a particular product.
You wanna hold my hand
A scale up like that tests the ability of a supplier to deliver quality and also manage financial viability, especially in a bad economic climate. And some suppliers may not be able to make it to the shore.
Take for instance, Shutham Electric that made the first lot of combination switches. “These are commercial not quality failures,” says a senior executive in a company that has purchased parts from Shutham. He believes that The Nano project required suppliers to invest a lot of money upfront and earn their profits once the large volume sales started to happen. Not every supplier could manage this switch in scale and ability to absorb losses in the initial phase.
This is not an attempt to put all the blame at the doorstep of Nano suppliers. “Blaming a supplier is the cheapest trick in the book,” says a senior automotive professional who has worked with global companies like General Motors and Chrysler. “An OEM bears full responsibility for selecting design, selecting supplier, validating and testing prototypes, ensuring proper assembly and finally having robust supplier quality processes to get the right parts in the door.”
Most critical component suppliers -- guys who make the engines, the transmission, gearbox et al -- say that the Tata Motors process for selecting vendors and testing their quality was exemplary. Almost 15 Tata Motors officials would observe the production process at a vendor and only when they were satisfied would the vendor be taken on board. After that there would be three audits: Self-certification, fortnightly audit and finally surprise audit. “If the surprise audit uncovers something the self-certification is automatically cancelled,” says a senior official at a critical component supplier for Nano.
History shows Tata Motors has a history of putting out cars in the market without resolving all teething issues. For instance, the first generation Indica had a serious starting problem. The Safari’s turbo plumbing hoses were of poor quality. And even the new generation Indica Vista had seen power steering pump issues and noises coming from the suspension. What does this tell us? The clearest explanation is that Tata Motors’ hasn’t achieved mastery in vehicle testing. And these capabilities take time to develop.
Let’s face it: Tata Motors began the transition from making trucks to passenger cars in the last decade and a half. Most importantly, suppliers have to also go through that learning curve. “You need rigorous process and you need people who will follow the process. Indians revel in jugaad, and getting things done at the last minute,” says a former employee.
Large companies abroad have a horizon of seven to eight years for a new model. This time frame allows them to thoroughly test the car.
Apart from planning, Tata Motors will have to develop a much more collaborative design process. One gets the feeling that this may not have happened. The reality is that the costing on this project meant most suppliers didn’t see much of a point in doing the Nano. Only after Singur did they think there was something worthwhile. And may be Tata Motors needs to get suppliers to buy into the project.
“Because of the secrecy involved around the project which you don’t want to be leaked to competition — which in turn is because of the poor IPR laws in the country — there is very little involvement of the supplier who manufactures parts as per the prints and technical specifications provided by the OEM,” says a supplier who has supplied crucial components on the Nano.
This can have unintended consequences. In 1998, in the SUVs manufactured by Tata Motors, there was a constant problem of oil leakage from the base of the vehicle. Tata Motors complained to the vendor that it was facing warranty issues and asked the company to look into the problem. But the vendor was not able to identify the problem for several months.
And then, one of the field teams which had a lot of experience working in the North American market, found that the part had been designed for near flat road gradients; Indian roads come with steeper sideward slopes and the vehicles typically tilt on the left side. Further, some bad drivers may have driven the vehicle with one side on pavements and the resultant tilt could have caused leaks. “So we just shifted the position of the drain hole to a different position. This is a dramatic difference in the standard of usage of a vehicle part and using it for a different terrain. If a vendor puts a normalised product, it will fail,” he adds.
Answer the customer
In all probability, it was a combination of all these factors -- supplier quality, lack of integration, design adaptation -- that has led to a faulty batch of cars. While solving the technical issue is a priority, Tata Motors will have to look at the way it has handled customer service.
For one, there has been no formal recall process. Even for the combination switches different dealers have different versions of how the company told them to proceed. “We were instructed by the company to check for combination switch problems on our stock and the cars that came in for routine servicing. We checked 100 cars and found only one had that problem,” said a Pune dealer. Another dealer in Mumbai says there was no communication of this sort at all.
Consider the case of Sawant’s car. When Sawant went to meet Concorde officials the day after his car burnt down, he was told by a Tata Motors representative that the car he was sold was a demo vehicle, which was never supposed be sold to him. Next day, a Tata Motors official spokesman confirmed this.
Now it is true that Sawant took the car out of turn, but since Concorde is a Tata Motors subsidiary, it would have been better if there were explicit instructions that a demo car not be sold. Of course, Tata Motors did pay Sawant Rs. 2.26 lakh as compensation. The reputational damage was more severe.
That’s something a landmark product like this cannot afford. Ever since Ratan Tata spoke about the concept it has caught the imagination of people all across the world. Now the company has to walk Tata’s talk. Not even a nanometer less would suffice.
The Ghost in the Machine
Preserve Capital
Learnings from Businesses in Hostile Territory
(Edited by Shishir Prasad)
Comments
0 comment