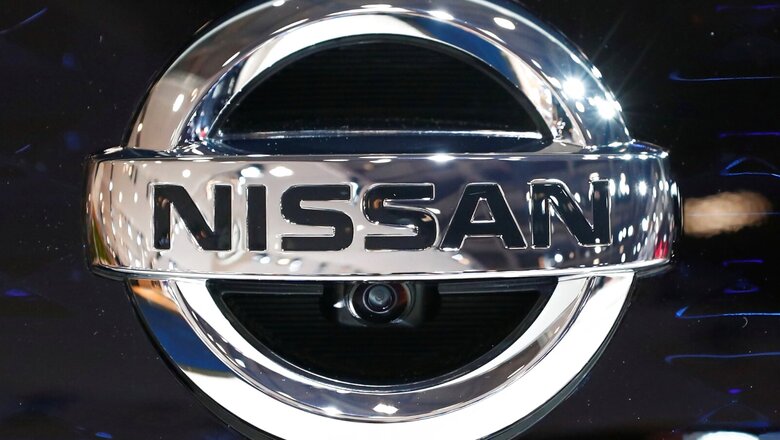
views
Nissan unveiled a prototype manufacturing facility for laminated all-solid-state battery cells on April 8. This particular battery is claimed to be a game-changing technology that the Japanese automaker hopes to bring to market by 2028.
The new facility is located in Kanagawa Prefecture, within the Nissan Research Center. The Japanese auto giant will use the facility to research the materials, design, and manufacturing processes that will be used in the production of all-solid-state battery prototypes. Later, the company intends to set up a pilot production line at its Yokohama Plant in fiscal 2024.
According to reports, given the benefits, Nissan anticipates using all-solid-state batteries in a wide range of EV segments, including pickup trucks. They have roughly twice the energy density of conventional lithium-ion batteries, a significantly shorter charging time, and can be made with less expensive materials.
All-Solid-State Batteries
The worldwide electric vehicle (EV) market has risen rapidly over the last decade. In 2019, there were roughly 7.2 million EVs on the road around the world, with that figure expected to rise to near 140 million in the next decade.
Lithium-ion batteries (LIBs) have been a key technology in the success of EVs among the various types of secondary batteries due to their high energy densities and long service lives. However, current LIBs are expensive and have a limited ability to deliver the performance needed to advance EV development.
Many academics and manufacturers are working to produce LIBs with higher power and energy densities to attain EV performance comparable to that of internal combustion engine vehicles.
This push to create more efficient and powerful LIBs has revealed some of the techniques’ safety issues. LIBs’ energy densities are increased by the close packing of electrodes and their short separation, but they also have a higher danger of exploding.
As a result, safe LIBs are required for the acceleration of EV deployment. Because of its high volatility and flammability, the liquid organic electrolyte (LE) is the component of a LIB most responsible for any combustion risk.
In this regard, all-solid-state batteries (ASSBs), in which solid electrolytes (SEs) are used as replacements for liquid electrolytes (LEs), are increasingly regarded as very promising next-generation battery systems. These batteries are also considered safer and more convenient as they have the possibility to charge in a short time.
The solid electrolyte, on the other hand, poses its own set of difficulties. It turns out that the interface between the positive electrode and the solid electrolyte has a high electrical resistance, the cause of which is unknown. Furthermore, when the electrode surface is exposed to air, the resistance increases, reducing battery capacity and performance.
A research team led by Prof. Taro Hitosugi from Tokyo Institute of Technology, Japan, and Shigeru Kobayashi, a doctoral student at Tokyo Tech, may have finally solved this problem in a recently published study.
The team has provided valuable insights into the manufacturing of high-performance all-solid-state batteries by developing a strategy for restoring the low interface resistance and unravelling the mechanism underlying this reduction—and this means that this battery could be revolutionary.
However, it is believed that all-solid-state batteries have the potential to significantly reduce the cost of EVs.
Nissan expects to reach $75 per kWh in fiscal 2028 and $65 per kWh thereafter using all-solid-state batteries. This would put EVs on par with gasoline-powered automobiles in terms of cost.
Read all the Latest Auto News and Breaking News here
Comments
0 comment