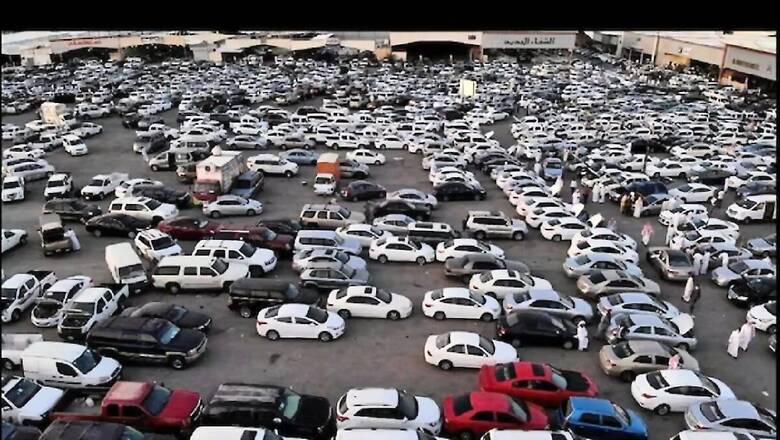
views
Written by Achal Saran Pande:
Nearly 50 per cent of commercial vehicle OEMs, 60 per cent of passenger vehicle OEMs, and 67 per cent of 2/3-wheeler OEMs claim to have implemented JIT practices. Despite these efforts, the auto industry still struggles with variability and stability in the ‘end-to-end’ supply chain, primarily manifested in the inventory levels with dealers.
What is JIT?
Just-In-Time (JIT), a production philosophy pioneered by Toyota in the 1970s, gained widespread popularity as Toyota’s growth accelerated. By the 1980s and 1990s, major OEMs globally adopted JIT. The substantial benefits reported by many international vehicle manufacturers drew the attention of large Indian OEMs, who also implemented JIT.
JIT implementation across the entire supply chain is expected to ensure high agility and flexibility to react to demand changes by promoting the flow of frequent, smaller orders. This approach is expected to prevent large swings in inventory levels, reduce inventory carrying costs, and improve reliability. It is also expected to enhance operational efficiency for all stakeholders — suppliers, OEMs, and dealerships. However, results have fallen short of expectations in India, as the promise of low and levelled inventory throughout the entire supply chain, crucial for all the other benefits to accrue in JIT systems, remains unfulfilled.
Inventory variability – An open secret
There are clear signs that the inventory benefits are skewed towards the OEMs. The median total inventory (RM+WIP+FG) for OEMs is only 27 days, while suppliers are stuck with 55 days. Recently, it was reported that car dealer inventories have soared to 50-55 days’ worth of sales, which is more than double the typical level of 20-25 days.
Additionally, the inventory throughout the supply chain goes haywire at times. For instance, post-COVID-19, when sales slowed down, dealer inventories swelled, and the market experienced a surplus. The OEMs took about 6-7 months to adjust production accordingly. Later it was succeeded by shortages as OEMs struggled to ramp up production to meet rising demand. This notorious ‘bullwhip’ effect is a common feature of every major sales slowdown. When inventory piles up with unhappy distributors, it grabs headlines, often.
Inventory expediting – A hidden pain
What is less visible to the public but more painful for OEMs is the struggle to ensure full kits at OEMs for production. Often, even in the immediate horizon (1-2 days before the schedule of production),15%-20% of the full kits tend to have one or more items missing, leading to poor production plan adherence, plan changes, and production delays. When the OEM production plan changes, it has a ripple effect on suppliers’ production plans, which also may have to change to align with OEM requirements. This results in capacity wastage and inventory pile-up when the OEM does not lift items made according to scrapped plans. This way of operations creates stress between OEMs and unhappy Suppliers.
The root issue?
JIT implementations are falling short for two reasons:
1. JIT is not end-to-end in the supply chain of these companies.
While many OEMs (60%) have implemented JIT practices in their processes, their supply chain partners have not been roped in JIT.
JIT is mostly limited to parts movement for assembly, not finished goods distribution.
What one can see in most auto supply chains is a hybrid of push and pull systems. Only daily inventory movement from suppliers to OEM plants and OEM production is as ‘pull’. Upstream at suppliers and downstream at dealers it’s a different story.
Nearly 100% of suppliers produce based on monthly forecasts and daily changes from OEMs, not true JIT.
Suppliers produce based on forecast-based monthly schedules sent in by OEMs. Forecasts are only 60%-80% accurate, which leads to issues like rescheduling of plans, missing components, and daily expediting at both OEMs & suppliers. So, the smaller suppliers tend to be forced to hold inventory and send in components as per daily demand of the much bigger OEMs.
Goods movement of 100% of the Indian OEMs’ dealers is not JIT-based but a target-based push system.
Downstream dealerships also order based on a combination of monthly/weekly forecast and targets set for them. However, when market demand fluctuates, dealerships experience mismatch of inventory – shortages and surplus of stock.
2. The boundary conditions wherein JIT works can easily be breached in the current auto industry environment (increasingly VUCA)
Most Indian Auto OEMs have to grapple with demand variations, especially at the SKU level, not only due to consumer changes but also due to shorter product cycles, regulatory changes, and rapid introduction of new models & components. This makes demand levelling difficult. In addition to variability in demand, the unreliability of supply also complicates inventory management. Supply chains for components typically involve multiple tiers of suppliers, and these are often spread in different regions or countries, which increases transportation times and the potential for delays due to customs, shipping logistics, or geopolitical issues.
This high supply and demand variability hinders strict adherence to a JIT-based approach (bin availability-based inventory movement). Therefore, the OEMs use JIT only for internal operations and inventory movement from suppliers, maintaining minimal inventory onsite while suppliers/dealers are required to keep ample stock.
Supply chain solution to manage variability
In environments with high variability, eliminating it completely, as JIT attempts, is impractical. However, variability can be significantly reduced using buffers. To implement a buffered system that responds agilely to market demand, follow these steps:
Build Buffers: Establish buffers at key locations, such as central warehouses (CWH) and suppliers, to replenish inventory based on consumption rather than fixed forecasts. This allows the OEM to absorb demand fluctuations and improve operational flow. Suppliers should transition to pull-based production, supplying the OEM based on daily inventory depletions.
Execution-Based Priority: Implement a priority method to manage demand and capacity variability. Set target inventory levels and use a colour-coded system (Red, Yellow, Green) to signal priority for production and dispatch, ensuring efficient responses to changing demand patterns.
Adjust Buffer Norms: Periodically adjust buffer norms based on intelligent sensing of demand changes. This includes tracking priority zones and using IT infrastructure to maintain high transparency and responsiveness in the system.
Conclusion
While JIT has its flaws, the lack of an effective ‘end-to-end’ pull system magnifies demand fluctuations, triggering sudden order shifts and bloated inventories. This scenario creates risks of disruptions and financial strain for dealerships and smaller players. However, by implementing a buffered ‘pull’ system, we create a supply chain that responds with agility while also protecting against variability in demand and supply without sacrificing flexibility.
In such a system, gone will be the days of inventory pile-up at dealerships during sales slowdowns. Every link in the supply chain can dance in harmony.
(The author is partner at Vector Consulting Group)
Comments
0 comment