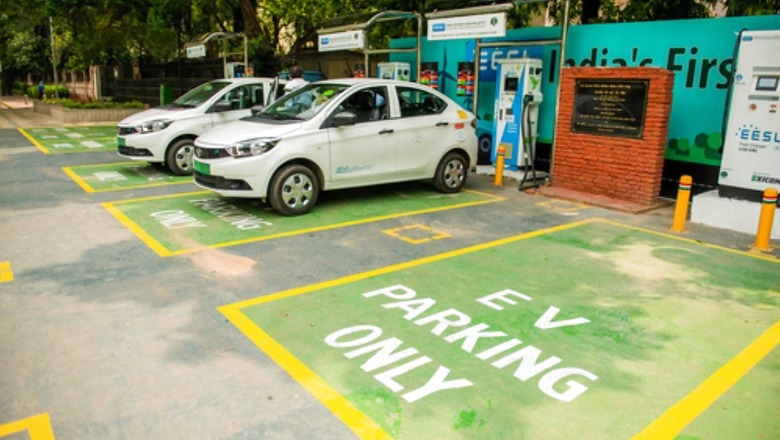
views
The Union Ministry of Road Transport and Highways recently announced that more stringent battery safety regulations for electric vehicles will take effect from October 1, pushing the industry to prepare for the big change while keeping new challenges in mind.
The ministry had established an expert committee led by Tata Narsingh Rao, Director of Hyderabad’s ARCI, in response to recent reports of fire incidents involving electric two-wheelers in various parts of the country.
Based on the committee report’s recommendations, the ministry issued amendments to requirements for motor vehicles with less than four wheels running on electric power, as well as amendments to specific requirements for four-wheeler EVs carrying passengers and goods.
According to the ministry, these amendments include additional safety requirements for battery cells, Battery Management System (BMS), on-board chargers, battery pack design, and thermal propagation due to internal cell short circuits leading to fire among others.
The ministry, in a statement, said the notification to mandate amended standards for the respective categories of electric vehicles effective October 1 is in the works.
The Industry
Applauding the latest move by the transport ministry, Naveen Dachuri, CTO and Co-founder of Yulu, told News18: “EV and e-mobility are at a nascent stage and any new products or categories will take time to mature. These measures will help bring back consumer confidence in EVs.”
According to him, the norms by the government will help increase the safety of batteries on three levels.
The increased number of stringent tests will improve battery pack efficacy as well as the safety, reliability, and performance of EVs. Additionally, Thermal Propagation Tests will aid in the detection and mitigation of battery fires. Along with this, the new standards ensure that the quality of Battery Management System (BMS) is improved.
Similarly, Smit Raturi, CEO of ChargeEZ, applauded the government’s move and said while there may be a few hiccups in the early days, in the long run, this would benefit consumers as well as the EV ecosystem as a whole.
“Beyond the new standards, as an EV charging player, we at ChargeEZ also believe that it is important to create awareness of safe EV charging practices among consumers,” he added.
Vikas Aggarwal, the Founder & MD of Ipower Batteries Pvt Ltd, said these amendments will impose more safety standards on all types of battery production and are a necessary step in ensuring a safer and smarter step in the fast-paced industry.
Challenges
While mentioning the challenges in the process of accepting such big changes and moving forward, Ipower’s Aggarwal said battery manufacturing will now undergo significant changes ranging from design, production, process, testing and validation.
“After such changes, any product should not immediately go into mass production as it needs to undergo rigorous lab and field testing for which the government must give all OEMs more time to incorporate all the necessary safety requirements in a phased manner,” he added.
Meanwhile, Yulu’s co-founder Dachuri said the main challenge that the industry is currently facing is lack of testing centres that are accredited to perform these tests.
“We believe that such policies should have more inputs and discussions with industry stakeholders for better implementation,” he noted.
However, Ganeesh Moorthi, CTO of Renon India, shared more technical details and concerns citing the recent amendments.
He said the changes include the traceability of cells used and understanding of the quality of the cells in terms of their actual capacity compared to the capacity of the manufacturer, which is accomplished through a process known as grading.
“Grading of a single cell would need a minimum of one hour of charging and one hour of discharging, totalling two hours. But ideally, we would like to do it at half speed,” Moorthi noted.
As mentioned by the industry expert, a typical battery pack contains hundreds of cells and in order to select or grade all of these 100 cells, 100 channels for testing all these cells simultaneously are required. This needs at least four hours of work. According to the standard, these cells must go through five cycles, which would take 20 hours before they can be integrated into a battery pack.
He said: “This is something challenging because unless we increase the number of machines for the channels, it is not possible to achieve this cycle time for the battery packs with the existing infrastructure. I think this could be one of the biggest or major challenges for the industry to immediately scale, either on the infrastructure or taking the cycle time to build the battery packs.”
He further added that cells are typically purchased in large quantities and if they lack the traceability required by the standard, there is an additional effort required to include that data on the cell, which will also take time.
“When it comes to the battery pack level, we have an IP 67 pack, which we believe will be a major challenge for every industry player who has been working with battery packs for two-wheelers,” Moorthi stated.
Production towards thermal runways is a major reason for many fire accidents, and this internal phenomenon that occurs due to internal short circuits at the cell level requires protection at the cell, module, and pack levels.
Citing the new norms, he said: “There needs to be an active fuse. It is a fuse that you see in any electric equipment to prevent any additional hazard happening at the cell level and then fused at the pack level which is something that would need a lot of changes in the architecture of the pack.
“It will be a bit of a challenge because the industry players in the market who have been there for a really long time have already invested in cooling or building a particular type of battery pack. It would be difficult for them to make changes as per the new standard that has come into the picture,” Moorthi said.
Additionally, he said when it comes to BMS, he said: “It requires particular or specific testing for it to be successful in its performance, and if it is not available with the industry players, it would be a critical bottleneck.”
When it comes to wireless communication standards, a near-field communication standard requires RFID, which is not available with more than 90% of the players on the market today, as per Moorthi. As a result, he believes that even with near-field communication, it would be a major challenge.
“As per the standard, we need to have both input and output capabilities, from BMS to RFID sensors. It needs to be tested again for recertification. So this is not available,” he stated.
In the case of charging, Renon India’s CTO said the charger also needs to have communication with the battery pack and it is something that most OEMs and manufacturers are doing.
According to him: “There are certain places where dump chargers are being used. They need to be replaced, and markets with dump chargers also need to adapt to these new standard requirements.”
“The problem here is that since most of the industry players are not the same as battery and charger manufacturers, there needs to be a lot of understanding between the two to get aligned to the new amendments. It would also need development time from both industries,” he added.
Moreover, according to the expert, thermal runaway methods with audio/visual warning are also a new area. He believes that this can be managed through alternative methods like sending the data to a mobile application and the mobile application sending notifications, warnings, or alarms through the communication front.
He said if this can be accepted as an alternative, it is also something which could ease the situation. “If there could be a specific protocol that could be developed for the communication front, that would be something that would be really helpful,” he stated.
Read all the Latest Auto News and Breaking News here
Comments
0 comment